|
|
Production Process and Facilities |
A typical production line for ceramic tiles is comprised of preparation equipment (which typically includes a miller (ˇ°Mixing and Grindingˇ±) and a spray dryer), a press (which is used for molding raw ceramic material), a glazing line (used to supply glazed materials to the pressed tiles), a kiln (used to harden (ˇ°Fireˇ±) the soft mixture of clay and minerals into a hard ceramic body by subjecting the mixture to high temperature) and packaging. |
|
The following chart sets out the major steps involved in the production process: |
 |
|
The procedures involved in the production of ceramic tiles are summarized below: |
|
|
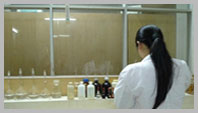 |
|
(i) Inspecting |
|
Raw materials for ceramic products consist mainly of clay (comprised of inorganic materials such as kaolin, flint and feldspar) obtained mostly from areas adjacent to the CompanyˇŻs facilities, such as Dehua county of Quanzhou city. Raw materials are inspected by quality control staff upon receipt. Batch calculations that take into consideration both physical properties and chemical compositions of the raw materials are performed to ensure that the right amounts are mixed. |
|
|
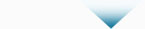 |
|
|
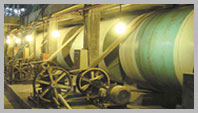 |
|
(ii) Mixing and Grinding |
|
After stringent checks on the quality of the clay and weighing, the raw material department mixes the clay as determined during inspection. The mixture is then sent to a ball mill where water is added to form a slurry for finer grinding. This process takes approximately 12 hours to complete. The slurry is then filtered and metallic particles are removed magnetically. The slurry is inspected at this stage for density, flow speed and water ratio. Although many competitors use stone ball millers, we use aluminum ball millers to grind materials. Aluminum ball millers have a higher initial cost, but have higher grinding speed and can better process stone chips existing in the slurry. The slurry is then moved to a 1,200 ton slurry pool. Based on production scheduled, portions of the slurry may be moved to smaller slurry pools where coloring materials can be added. The mixture in smaller slurry pools are churned for approximately 24 hours to keep quality and color consistent in the end product. |
|
|
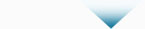 |
|
|
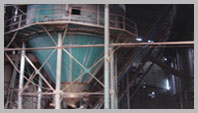 |
|
(iii) Spray Drying |
|
A spray dryer is then used to remove most of the water content in the slurry to obtain granules with the required moisture level for processing. The slurry is pumped into an atomizer, consisting of a rapidly rotating disk or nozzle where droplets are formed. The droplets of the slurry spray are then dried by a rising hot air column, forming small free-flowing granules of a standard size and specific moisture content which is used in the next stage. The stream of gases used to dry the slurry can be at temperatures as high as 1,100ˇăC. The granules are then moved to and held in steel containers (ˇ°hoppersˇ±) for over 24 hours to ensure consistency and uniformity of granule size and color. |
|
|
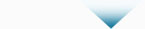 |
|
|
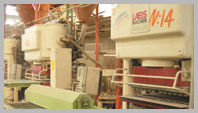 |
|
(iv) Molding |
|
The granules flow from a hopper into the mold die where they are compressed by steel plungers and then ejected by the bottom plunger in varying sizes based on specifications. The automated presses used operate at pressures as high as 1,600 tons. The ceramic bisque, a shaped non-fired ceramic tile, is then passed through to the dryer to remove most of the remaining water content present in preparation for the firing and/or glazing stages. The tiles are fed into the dryer and conveyed horizontally on rollers, at temperatures of 250ˇăC for approximately 15 to 25 minutes based on tile type. |
|
|
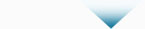 |
|
|
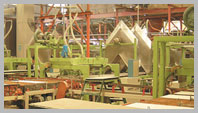 |
|
(v) Glazing |
|
Glazing involves applying one or more coats of glaze, comprised mainly of silica and other coloring agents such as iron, chromium, cobalt or manganese, onto the tile surface. The dried ceramic bisque is then sent to the glazing station where a design and/or color is added. The glaze concentration and glazing quantity is controlled by computers to avoid chromatic aberration and lack of uniformity. Not all products, such as porcelain tiles, require glazing. |
|
|
|
|
 |
|
(vi) Firing |
|
After molding and/or glazing, the ceramic bisque is fired in a kiln. Typically, the temperature in a kiln is about 1,200ˇăC and the firing process takes less than one hour. The entire firing process is monitored and controlled by computers. The Company currently has nine firing lines in its production facility. |
|
|
|
|
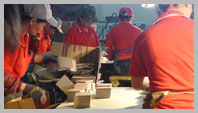 |
|
(vii) Packaging |
|
After the firing process, tiles are inspected for quality. Tiles which pass inspection are packaged and moved to the storage facility. |
|
|
|
|
|
China Ceramics Co., Ltd.
Edmund Hen, Chief Financial Officer
info@cceramics.com
Junbing Industry zone, Anhai town,
Jinjiang
Fujian,PRC, 362261
Investor Relations:
Precept Investor Relations
David Rudnick
Direct Line:: +01 917-864-8849
David.Rudnick@preceptir.com |
|